Rental of MIG/MAG welding machines
Within the port of Antwerp, Antwerp Welding Supply nv has an extensive range of MIG/MAG welding machines for rent for many years. We are known for our many years of expertise and always ensure a smooth follow-up, service and delivery for every project or for every customer!
Our offer consists of various Kemppi MIG/MAG welding machines with different technical specifications; from 220V to 380V, from 200A to 500A, gas-cooled or water-cooled,...
MIG/MAG welding is mainly known for its ease of use and speed of welding. This welding technique is perfect for quick/short repairs or for processing large steel structures. The automatic supply of the welding wire ensures that you can hold the welding torch with one hand and that you can guide and support the torch with the second hand.
Rental offer
Rental range of MIG/MAG welding machines
Kemppi gascooled MIG welding machines
Model / type | Daily price | Weekly price | Monthly price |
MIG/MAG 220v - 200A | from 27,50 € |
from 68,75 € |
from 206,25 € |
MIG/MAG 380v - 250A | |||
MIG/MAG 380v - 300A | |||
MIG/MAG 380v - 320A |
Kemppi watercooled MIG welding machines
Model / type | Daily price | Weekly price | Monthly price |
MIG/MAG 380v - 400A | from 51,00 € |
from 127,50 € |
from 382,50 € |
MIG/MAG 380v - 500A |
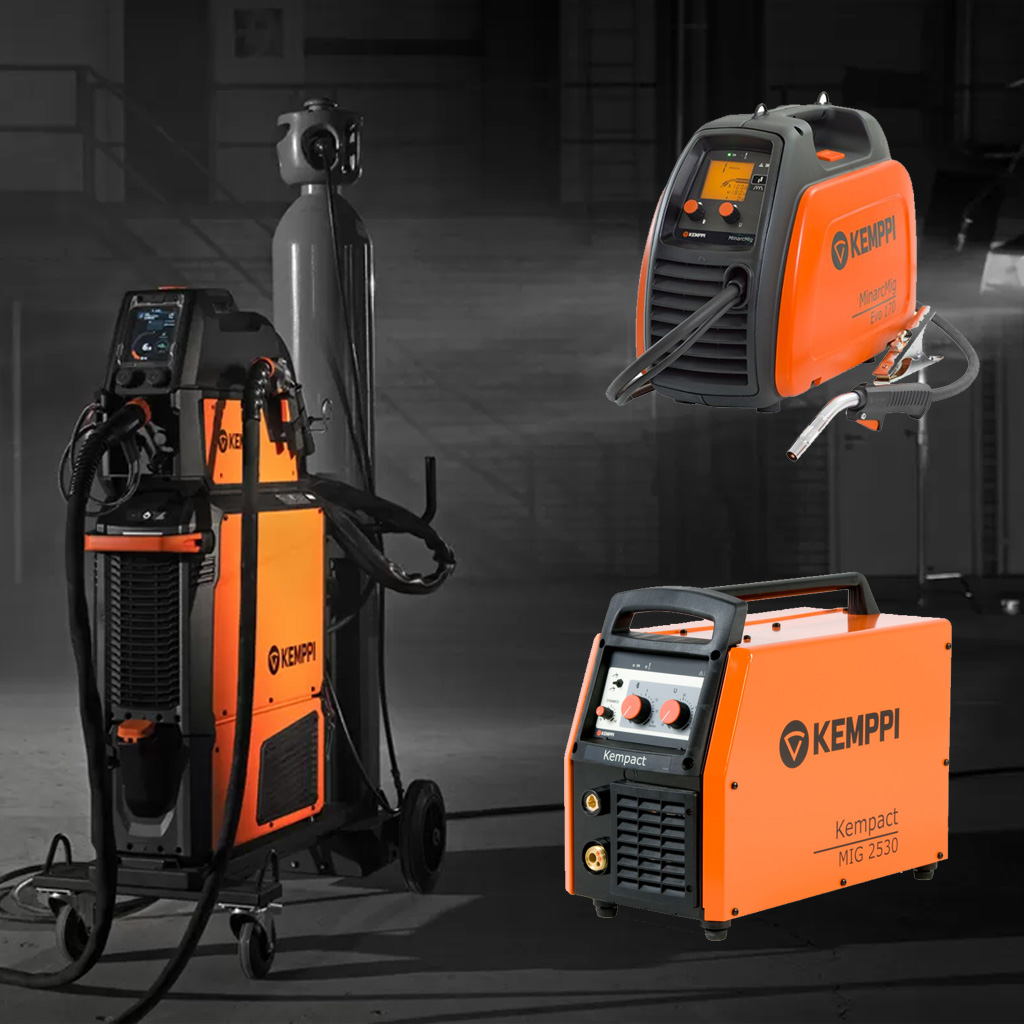
Questions?
Frequently asked questions
What's included?
All our MIG/MAG welding machines come with:
- Ground clamp 5 meters
- MIG torch 3 or 4.5 meters
- Pressure gauge for the gas cylinder
Machines are supplied without gas and welding wire.
Also have look at our extra accessories.
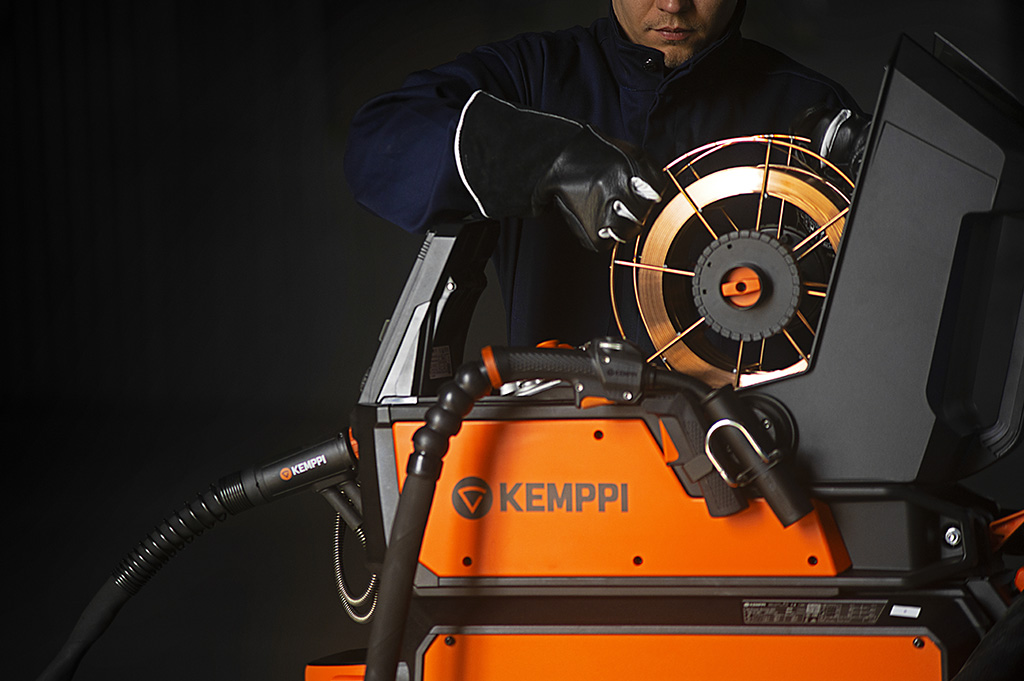
What's the difference between MIG and MAG?
The big difference between MIG welding and MAG welding is the type of shielding gas you use: Inert or Active. The welding process remains the same, which means that MIG/MAG welding is seen as the same technique.
With MIG/MAG welding, the filler material or welding wire comes out of the welding torch automatically and continuously at the speed you choose. After all, you work with a pre-placed water coil in the device to continue to provide the additive material.
Partly because of this, it is a popular and very fast welding technique in the metal industry because of its simplicity with large welding works and surfaces.
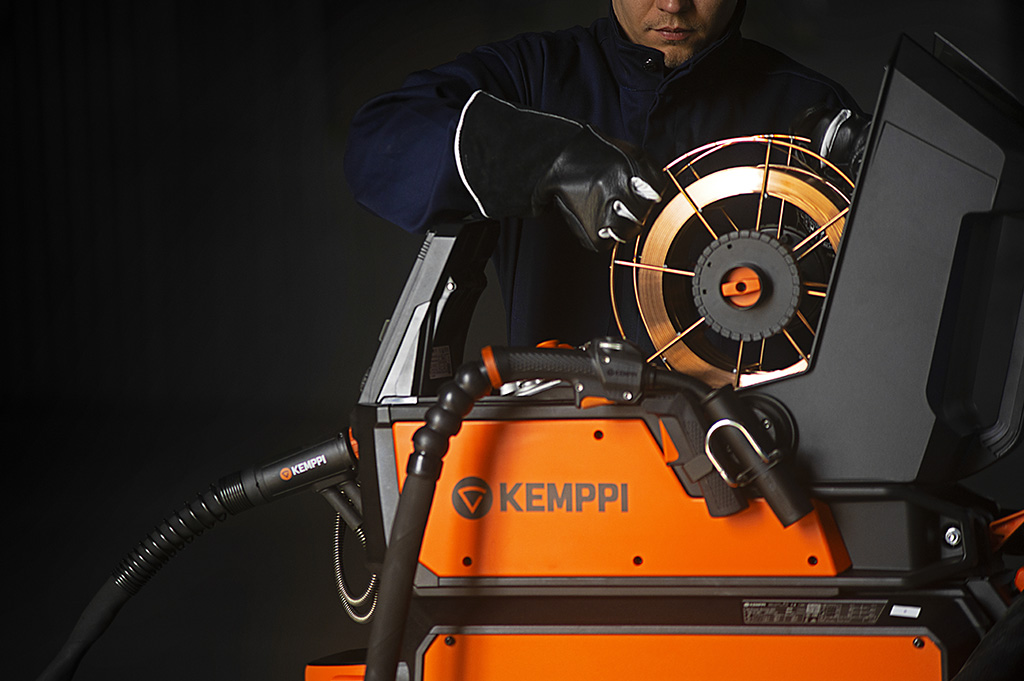
How does it work?
A MIG/MAG welding machine works with a constant electrical voltage, which creates a plasma arc between the welding wire and the workpiece. The workpiece is heated and the materials to be welded melt together. The welding wire acts as an electrode and filler material, so that you can work quickly and easily.
The welding wire is placed in the device and continuously mechanically fed to the torch. Depending on the work, the person will set the speed and current to place the most ideal weld. The function of the added gas is to protect the molten pool against overheating of the materials.
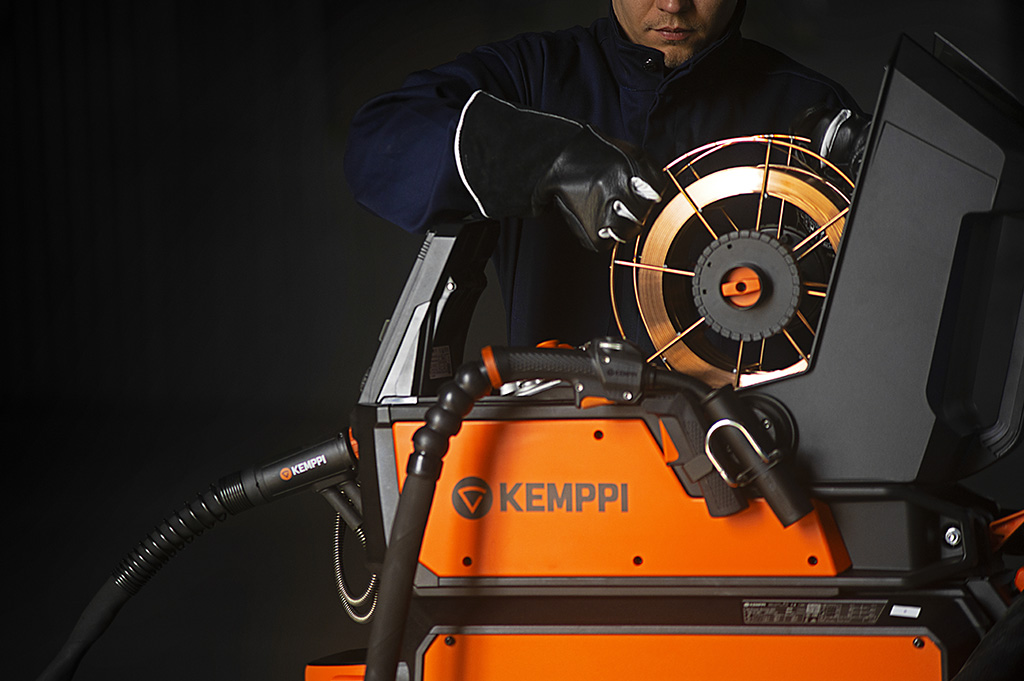
When to use it?
Because MIG/MAG welding works quickly and ensures a high-quality result, it is widely used in the (metal) industry. The welding process is mainly used in places where high productivity is important.
In the meantime, there are also options for working with a gas-filled welding wire, so that you no longer need an external gas bottle. Combined with a compact and portable welding machine, it also makes this a lot more attractive for work on the move, where mobility and speed are important.
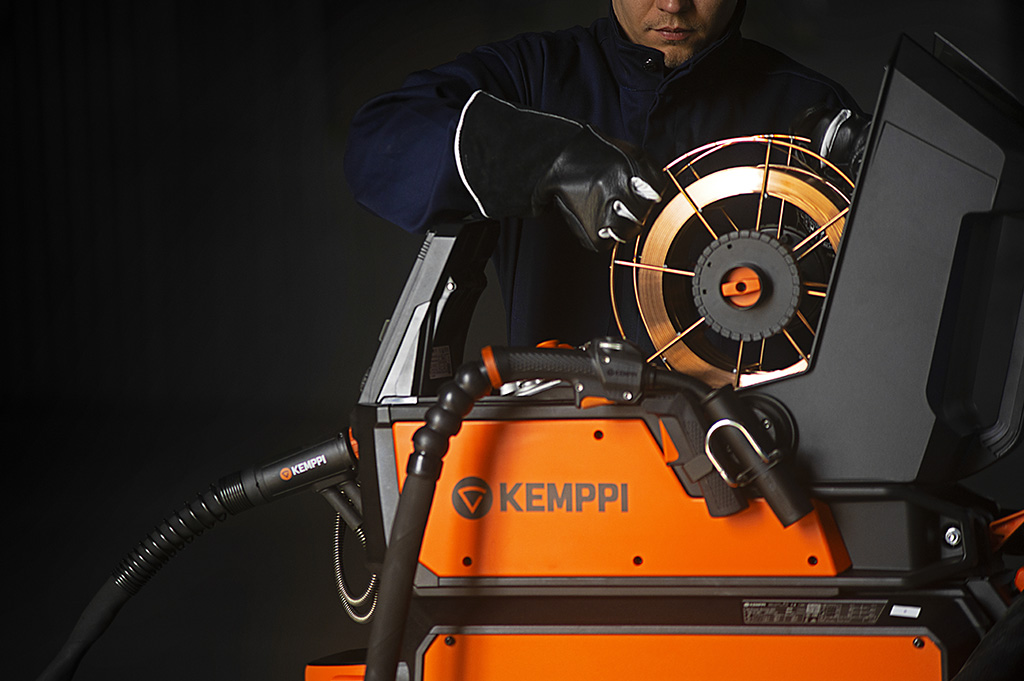
What do you need?
You need the following minimum items for MIG/MAG welding:
- A welding machine with support for MIG/MAG welding
- A ground terminal
- A MIG/MAG torch
- Welding wire on coil
- Gas (or gas-filled welding wire)
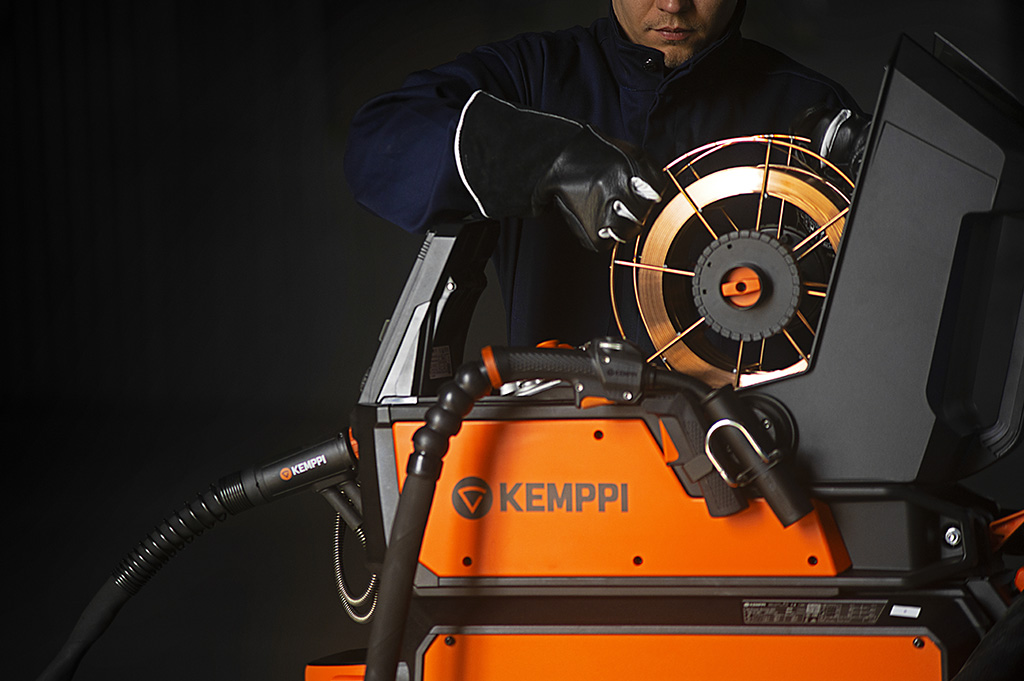
What materials can you weld?
You can weld all types of steel and stainless steel of different thicknesses with this technique. However, for aluminum welding, the welding machine must have a pulse function. The current level then changes between base current and peak current, so that you can weld thin and vulnerable material such as aluminum in a very controlled manner, without the top layer burning.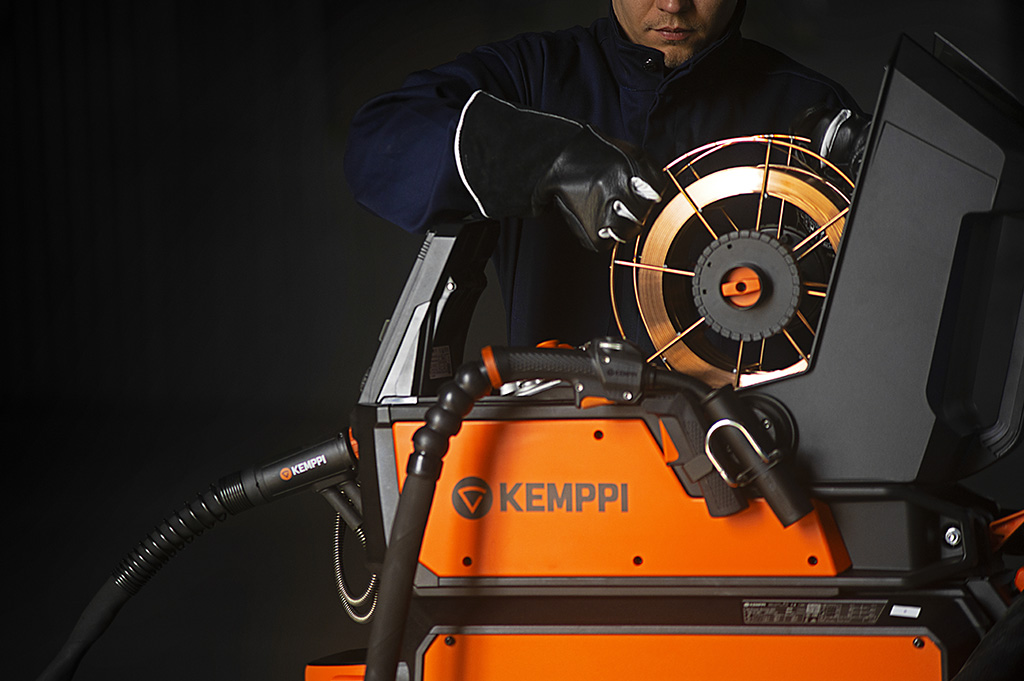
What are the advantages?
The main advantages:
- Quick and easy technique
- Many possibilities in use of materials
- Automatic and constant supply of filler material
- Useful for large welding jobs
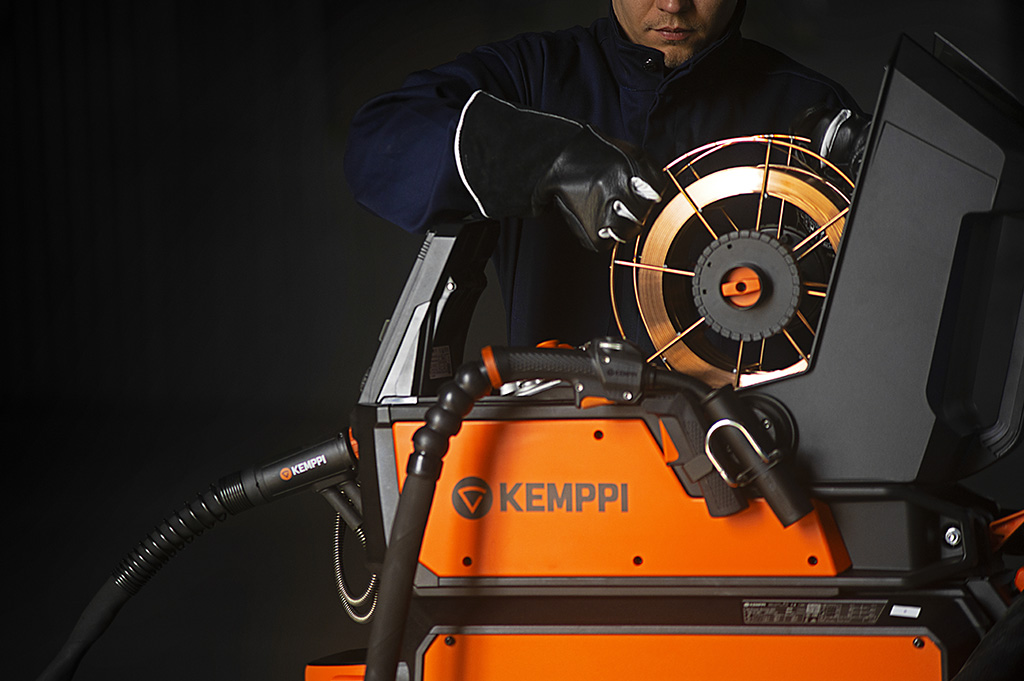
What are the disadvantages?
The main disadvantages:
- Spatter may occur near the welding work
- Difficult to use outdoors due to the need for the shielding gas
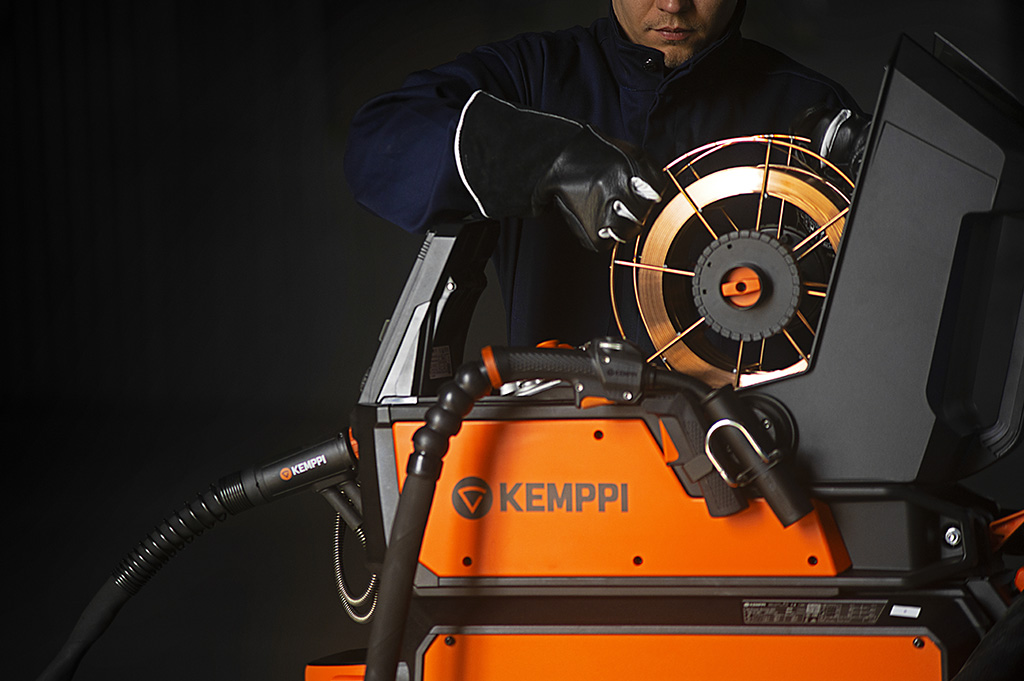